By Jane Fyksen
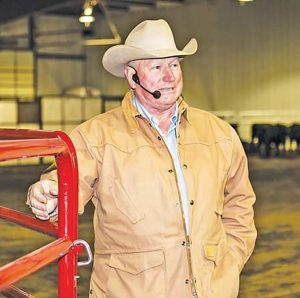
Who wouldn’t wish handling cattle would go like clockwork, especially when it seems like it rarely does? Too often working cattle stresses both man and beast, straining marriages and sometimes even resulting in injury to an animal, or worse yet, a cattle handler.
Handling cattle needn’t be an exercise in anger management, according to Ron Gill, Texas A&M University Livestock Specialist.
“Low-stress cattle handling is not establishing “kumbayah” with the cow,” Gill said.
“It has nothing to do with being gentle and slow,” he said. “It has everything to do with getting them to understand what I’m asking. Are they doing what I’m asking when I ask?”
“It’s also understanding that the best way to communicate with cattle is to tap into their sight,” he said. Thus low-stress handling can only be accomplished with a complete understanding of how a prey animal like a beef cow responds to line of sight — and how what cattle see influences their movement and behavior.
A successful stock person keys on a cow’s head – the 4 to 6 inches occupied by its eyes and ears, as opposed to trying to push the body around or slapping its rump. The cow truly doesn’t know what a person is asking from that. She’s going to turn around to see what’s going on behind her, or she’ll circle around the handler to try to see what he’s asking. She’s also apt to go in the wrong direction.
Looking into the cow’s eye adds pressure, similar to how a good stock dog controls livestock by staring — or what’s commonly referred to as “giving eye.”
Noise – particularly a human voice – is usually stressful for cattle and only marginally successful in obtaining the desired result. Sound should only be used as a backup method to move cattle, when line of sight and the handler’s position in relation to the animal isn’t adequate. Similarly, distracting sounds can shift cattle’s focus away from the direction the farmer wants them to go.
Gill said touch is really only useful when cattle are confined and additional stimulus is necessary to encourage them to respond. “Effective touch does not include sorting sticks or paddles that give cattle a jolt nor whacking them with anything,” he said.
There are five things a producer should know about cattle behavior, he said, for easier and speedier cattle handling.
1. Cattle want to see the herds person – Cattle have excellent peripheral vision with two exceptions – a large blind spot directly behind them and a small one in front of them. Working cattle from behind encourages them to turn to see the handler. When working from behind, to keep cattle from turning, stay in their sight by moving from side to side.
2. Cattle want to go around the handler – This is also related to cattle’s desire to maintain visual contact. The handler needs to position himself so when cattle do go around him, they’re pointed directly at the intended gate or destination. They’ll think it was their idea to go there, Gill said.
3. Cattle want to be with other cattle and attempt to go where they see other cattle – Prey animals, which cattle are, have a herd mentality because there is strength in numbers. A producer can take advantage of that natural instinct by working the cattle at the front of a group. Start the front cattle moving and those in back will follow, Gill said.
4. Cattle can only process one thought at a time – If cattle are thinking about anything other than what the handler is asking them to do, change their focus before putting pressure on them.
5. Cattle want to remove any pressure they feel – Their instinct is to return to the last-known place that was safe or comfortable. A producer can use this to his advantage when sorting and moving cattle from one pen to another by incorporating a “return box” — or what’s commonly referred to as a “Bud Box” after its designer, the late Bud Williams.
Gill said a Bud Box is a facility design that allows a handler to position himself so cattle flow out of the box into either a crowd alley leading to a chute or to a single-file trailer load-out. The box is for flow-through; cattle shouldn’t be cooped up in the box, waiting to be sent into a crowd alley or to the trailer.
“Bring them in and let them flow back out immediately,” Gill said. “Remember, the crowd alley will normally not be empty when additional cattle are brought through the box. To maintain flow, it will be necessary to add additional cattle while one or two stand in the crowd alley waiting processing. Consequently, the length of the crowd alley is important. Ideally the crowd alley would be long enough to hold an adequate number of cattle for processing, while more cattle are brought through the box – without disrupting flow.”
Gill said the livestock industry has migrated to a crowd alley that starts to curve at the entrance from a tub or box. Instead, he said, the exit from a tub or box and entrance into the crowd alley should be straight for at least two mature-cow body lengths. That allows cattle to flow by tricking them into not thinking they’re entering a dead-end crowd alley. Keep it straight for at least 12 feet and then start a curve if space is limited. Otherwise a long straight crowd alley works best for processing cattle, he said.
Most cow-calf operations need a box at least 12 feet wide and 20 feet deep. A width of 14 feet is too wide for working livestock on foot; it’s for working cattle on horseback.
“The box needs to be deep enough to allow the cattle to flow to the back of the box, let the handler close the gate and get in position before the cattle transition out of the back of the box,” Gill said. “Just like a tub system, never overfill the box. Success depends on the flow into, transition and flow out of the box.”
It’s critical the end of the box be translucent so cattle can see light and build speed when entering the box. Entry speed facilitates the transition and correct flow out of the box. However, opt for solid panels on the box’s entry gate and sides of the box closest to the crowd alley and load-out exits. That will minimize distractions. Load-out and crowd-alley exit gates should also open flat against the sides of the box.
Contact Gill at rgill@tamu.edu or 979-845-3579.